Fluorite Ore Processing Flowsheet and Washing Plant
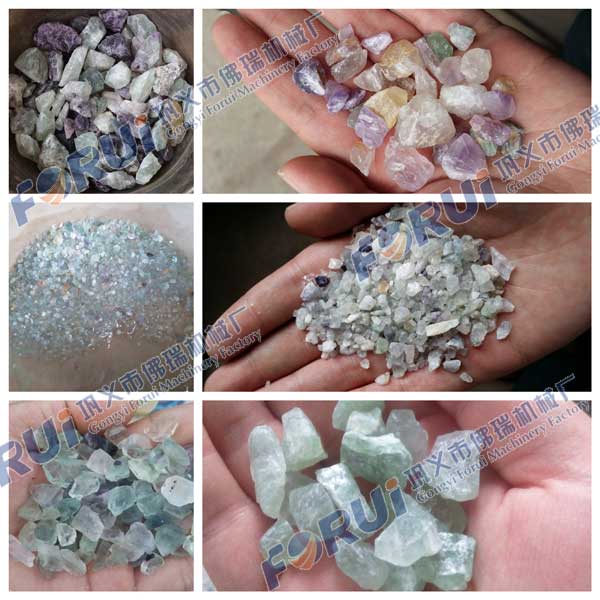
The main component of fluorite is calcium fluoride, which is used in metallurgy and chemical industries. Fluorite beneficiation solutions include froth flotation and gravity separation. Froth flotation is mainly for finely disseminated fluorite ore and is the only way to obtain chemical-grade fluorite powder. Fluorite flotation equipment mainly includes crusher, ball mill, classifier, mixing drum, flotation machine, etc.
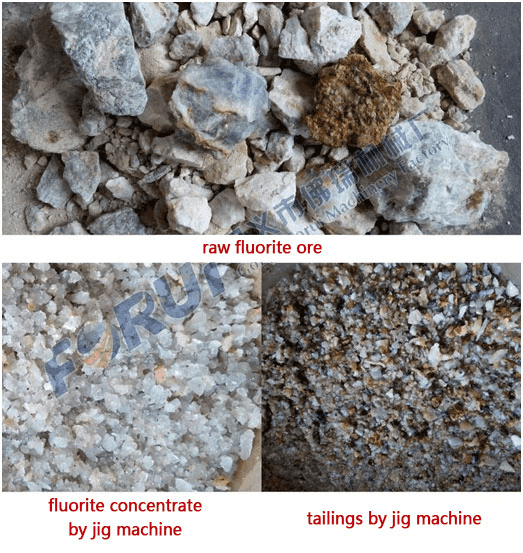
Gravity separation is only used for coarse-grained fluorite and is the only method to obtain metallurgical grade fluorite granule or lump. The core equipment of fluorite gravity separation is a mineral jig machine. It can process fluorite ore with a particle size of 0-50mm. Related auxiliary equipments are crushers, vibrating screens, etc.
If you are interested in a fluorite ore gravity separation plant, please contact us. phone/whatsApp:+8613592513050.
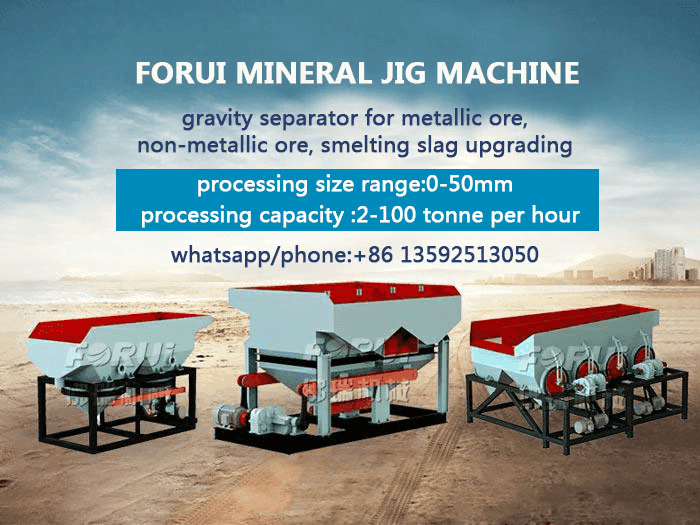
Here we introduce you to the gravity separation process of fluorite ore.
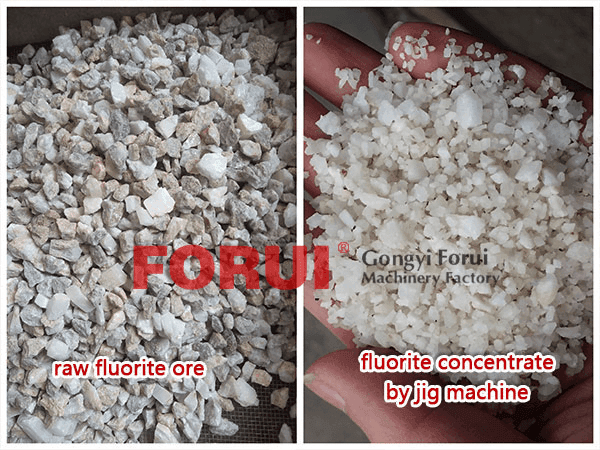
Fluorite ore gravity separation process flow chart
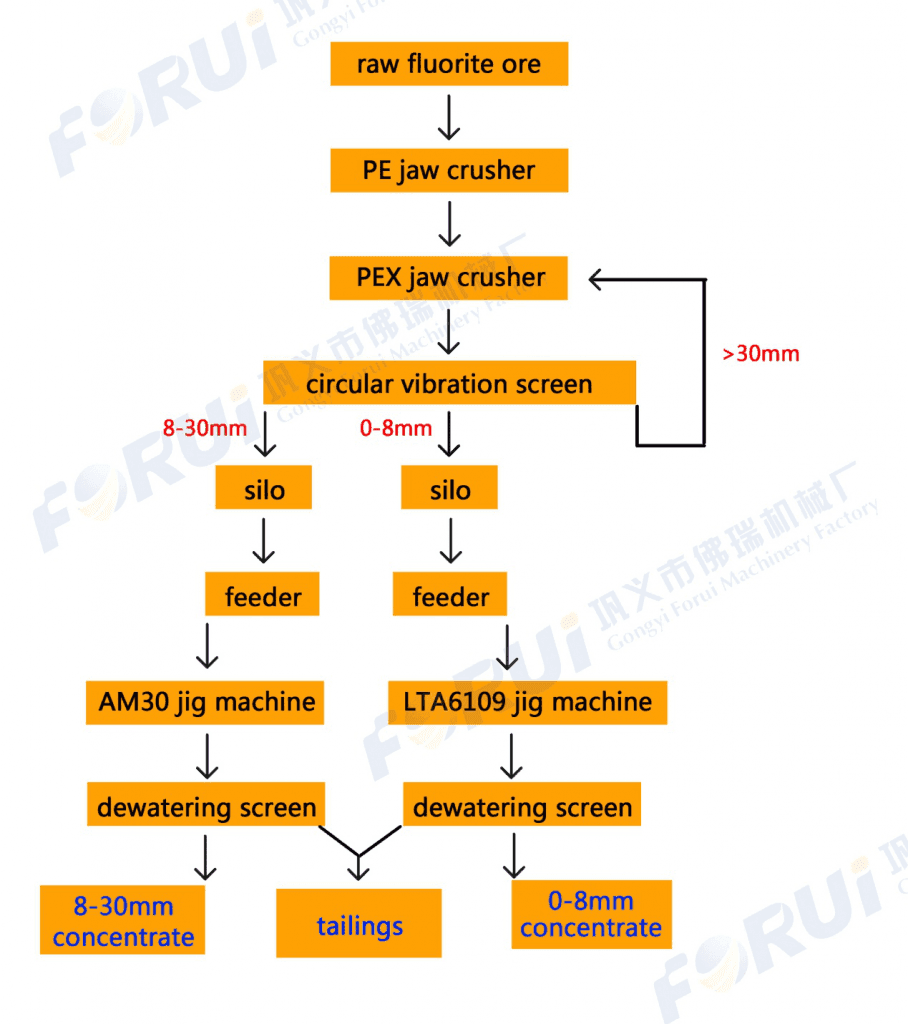
Fluorite ore gravity separation process video
1.Crushing process
Fluorite ore is brittle and fragile. In the crushing process, it is important to crush the raw ore to a suitable particle size range while avoiding too many powders caused by over-crushing.
The crushing process is simple and efficient by using PE series and PEX series jaw crushers to coarsely and finely crush the ore.
2.Screening process
The screening equipment of fluorite ore should be determined according to the characteristics of the ore. If the raw ore contains a large amount of mud and has strong viscosity, trommel screens should be used to reduce the clogging of the sieve holes. The trommel screen working with spraying water can also play a role in ore washing. If the raw ore does not contain mud and the water content is very low, a circular vibrating screen should be adopted.
The screening process divides the crushed materials into three levels, 0-8mm particle enters the silo ②, 8-30mm enters the silo ①, and the material larger than 30mm returns to the crushing process to be re-crushed.
3.Concentrating process
For fluorite ores with obvious crystals, clear boundaries between fluorite and gangue, or monomer dissociation, it is the best choice to use a jig machine to produce metallurgical grade fluorite, which not only has low investment in beneficiation equipment, but also low operating costs. At the same time, there is no pollution to the environment.
For finely disseminated fluorite ore, froth flotation is the correct method.
As mentioned earlier, the jig machine is the core equipment for fluorite ore upgrading. In this process, we use two different models of jig machines to processing the 0-8mm and 8-30mm fluorite ore respectively. AM30 jig machine for 8-30mm fluorite and LTA6109 jig machine for 0-8mm fluorite.
- Dehydration process
The jig machine uses water as the medium, so the concentrate and tailings discharged by the jig machine have a large water content, which requires simple dehydration. For this dehydration process, we recommend the use of high-efficiency dewatering screens, which can greatly reduce the surface moisture of the minerals. The excess water is returned to the circulation tank for reuse.
Here are some of our fluorite ore processing plant working site:
Responses