What Are the Common Preparation Operations for Mineral Processing
The preparation operations for mineral processing includes crushing, screening, grinding, grading. The main purpose is to separate useful minerals from gangue minerals to prepare for mineral processing. Sometimes this preparation involves dividing the material into appropriate grain sizes in preparation for the dressing operation.
This is a production line we designed for scheelite ore processing in Nigeria. Let’s take a look at its preparation operations for mineral processing.
1. Crushing of Preparation Operations for Mineral Processing
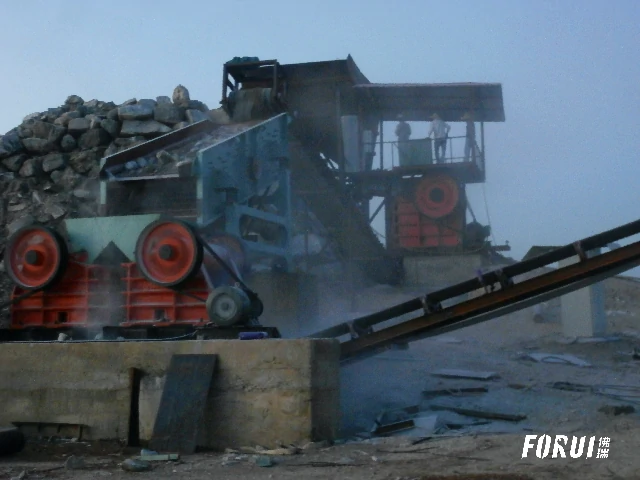
The ore blocks that come out of mines are very large. The maximum size of open-pit mining ore block is about 1000mm~1500mm. The maximum size of ore blocks mined underground is 300mm~600mm. Ore of this size cannot be processed directly, because the useful minerals in them are closely associated with gangue minerals. To separate the ore from each other, the first thing to do when the ore is sent to a concentrator is to break the ore to a certain size and then feed it into a mill to grind it up.
The type of crusher used in the concentrator mainly depends on the ore properties, the concentrator’s production capacity and the particle size of the crushing products. The coarse ore crusher is usually used for crushing. Jaw crusher, high efficiency crusher and roller crusher are commonly used in the medium and fine crushing operations. When crushing soft minerals, such as clay or coal, an impact crusher (such as an impact crusher and a hammer crusher) is usually used.
2. Screening of Preparation Operations for Mineral Processing
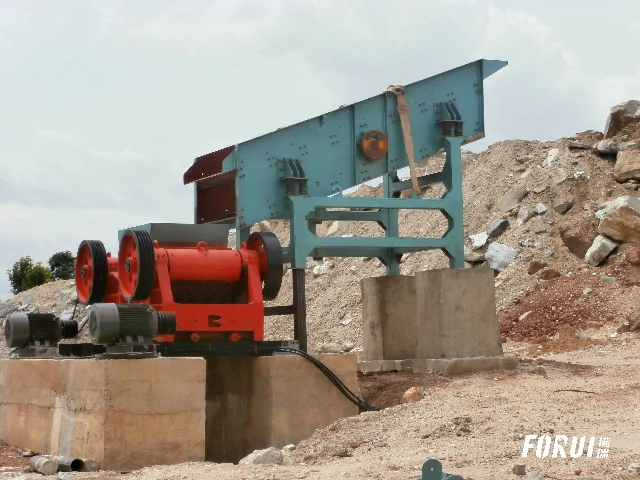
The process of separating loose material into different grain sizes through a screen is called screening. In concentrators, screening operations are usually used in conjunction with crushing operations.
Before the ore enters a crusher, the product whose particle size has met the requirements is screened in advance. This screening is called pre-screening. It can not only prevent the excessive crushing of ore, but also improve the productivity of the crusher. When the ore water content is high and more powder ore, it can avoid blocking crusher.
After the ore has gone through the crushing stage, screening equipment is used to check the particle size of the crushing products, so that oversized ore is returned to the crusher for crushing. This screening is called inspection screening. It can give full play to the processing power of the crusher.
3. Grinding
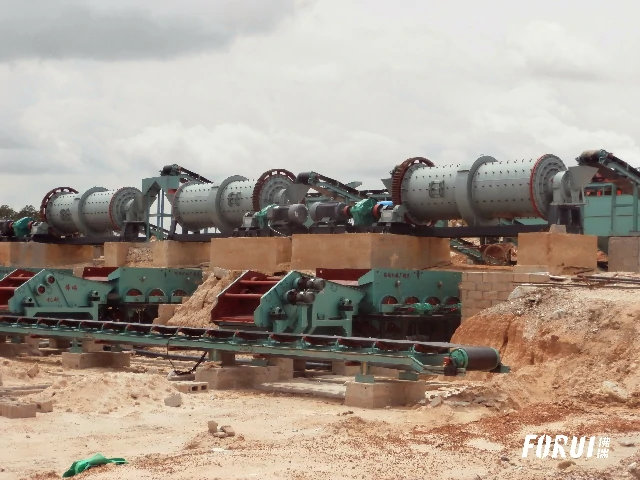
Grinding is the continuation of the crushing process. The aim is to separate most of the useful mineral particles in the ore into monomers. Make its particle size meet the requirement of ore dressing operation, so as to carry out ore dressing operation smoothly.
The milling operation is usually carried out in a cylindrical mill. The cylinder body is generally equipped with grinding media, such as steel ball, steel bar or gravel, and so on.
The ball mill body is equipped with steel balls (or iron balls). The rod mill body is equipped with steel rods. The gravel mill body is filled with gravel. If the mill is not filled with other media, only the ore itself is used for grinding, then called no medium grinding machine or called self-grinding machine. The self-grinding machine is formed by adding the right amount of steel balls. The specification of the mill is expressed by the diameter of the barrel multiplied by the length.
Grinding operations is mainly wet grinding, and generally with the classification unit into a closed cycle. But for the area of water shortage and some water-repellent process (such as cement plant, asbestos plant or some dry mineral processing process), there are also the use of dry grinding. No matter which type of mill is used for grinding, their principles are basically the same during the grinding process. They use the grinding medium (or the ore itself) to impact and grind the material.
4. Grading
In the medium (water, air, etc.), the process in which the material is divided into several different particle size levels according to its settling speed is called grading. The purpose of grading is the same as that of screening, which is to divide the ore group into different grain size levels, but their working principle and the grain size characteristics of the product are different. The screening is strictly separated according to the geometric size (mesh size). The classification is separated according to the different settling velocity of the material in the medium.
In the grinding operation, the grading operation is usually used to coordinate with it, so as to separate the qualified material in time. After using this operation, not only can avoid excessive crushing of the product, but also can improve the grinding efficiency.
The classification equipment used in the milling operation of concentrator includes mechanical classifier and hydrocyclone. The most used mechanical classifier in concentrator is spiral classifier, as for rake classifier, floating trough classifier, has been gradually phased out. In the tungsten and tin gravity concentrator, in order to reduce the grinding process of excessive crushing, the sieve and rod grinding mechanism are often used to form a closed cycle.
With the above preparation operations done, then we can begin the most important mineral processing. Next time I will share some common mineral processing operations.
This time we shared ‘What Are The Common Preparation Operations For Mineral Processing’. Next time we’ll share ‘What Are the Common Mineral Processing Methods‘.
Gongyi Forui Machinery Factory, founded in 1986. We are one of the leading suppliers of beneficiation equipments in Asia. Don’t hesitate to Contact Us, if you have any question of beneficiation. And welcome to visit our company. Gongyi Forui Machinery Factory dedicated to serve you!
Yeah such a nice post , i share some details it may be help you. I found an emergent mining and mineral processing company with a primary focus on the natural resources of Afghanistan. And they affiliate company in Afghanistan is 7COLOR MINERALS.